Support Equipment
Commercial Dehydrators offers a complete line of support equipment to compliment your dehydrator systems. Below are some of these products, please contact us for more information on anything listed here.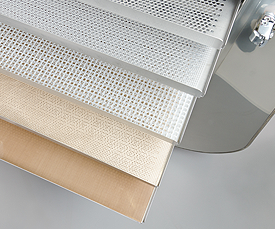
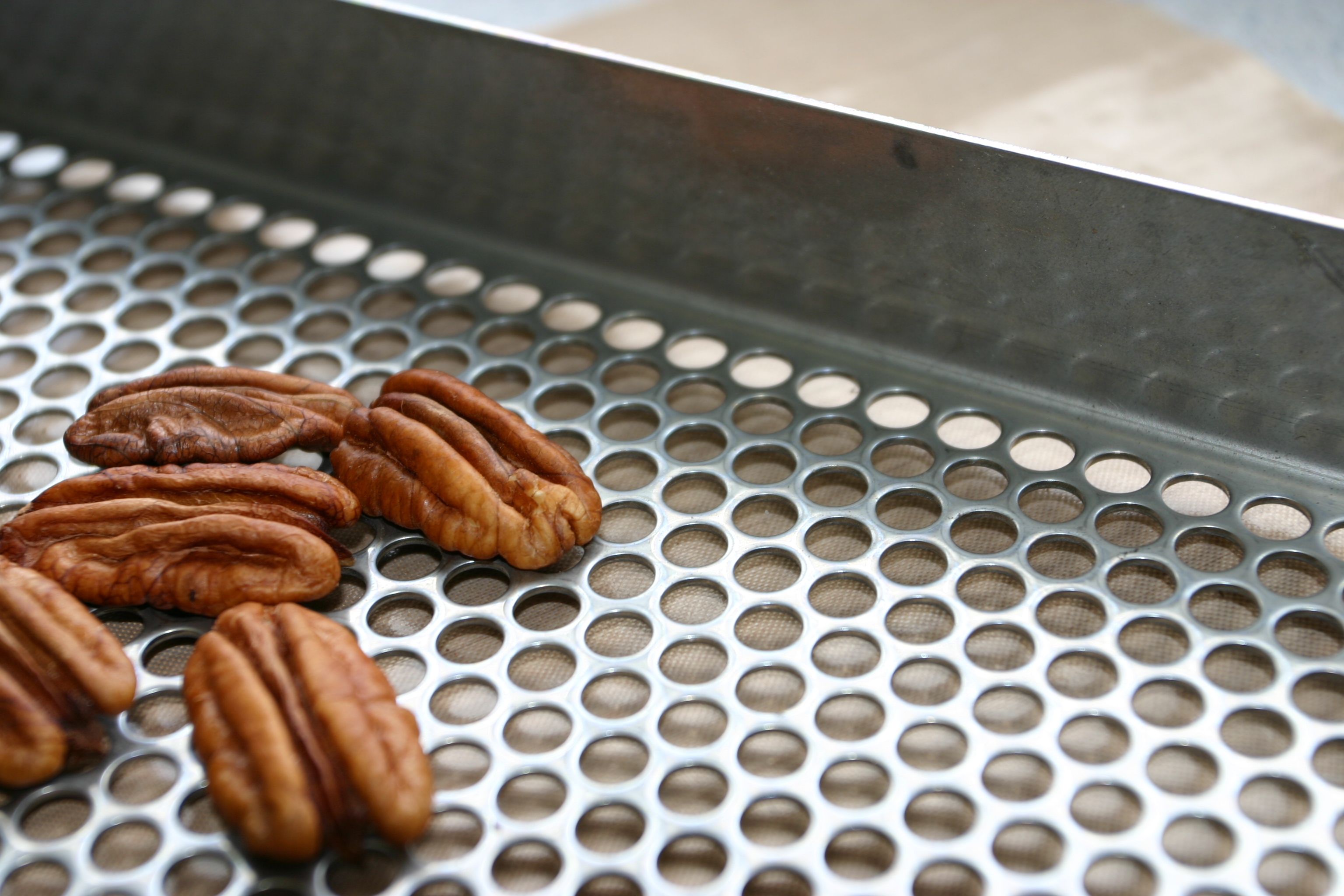
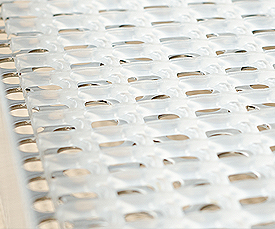
TRAYS AND LINERS (SOLD SEPARATELY)
Commercial Dehydrator has sourced many options for trays and liners to support your product use. These items can be purchased at any time separately. Some items available in bulk. Ask for more details.
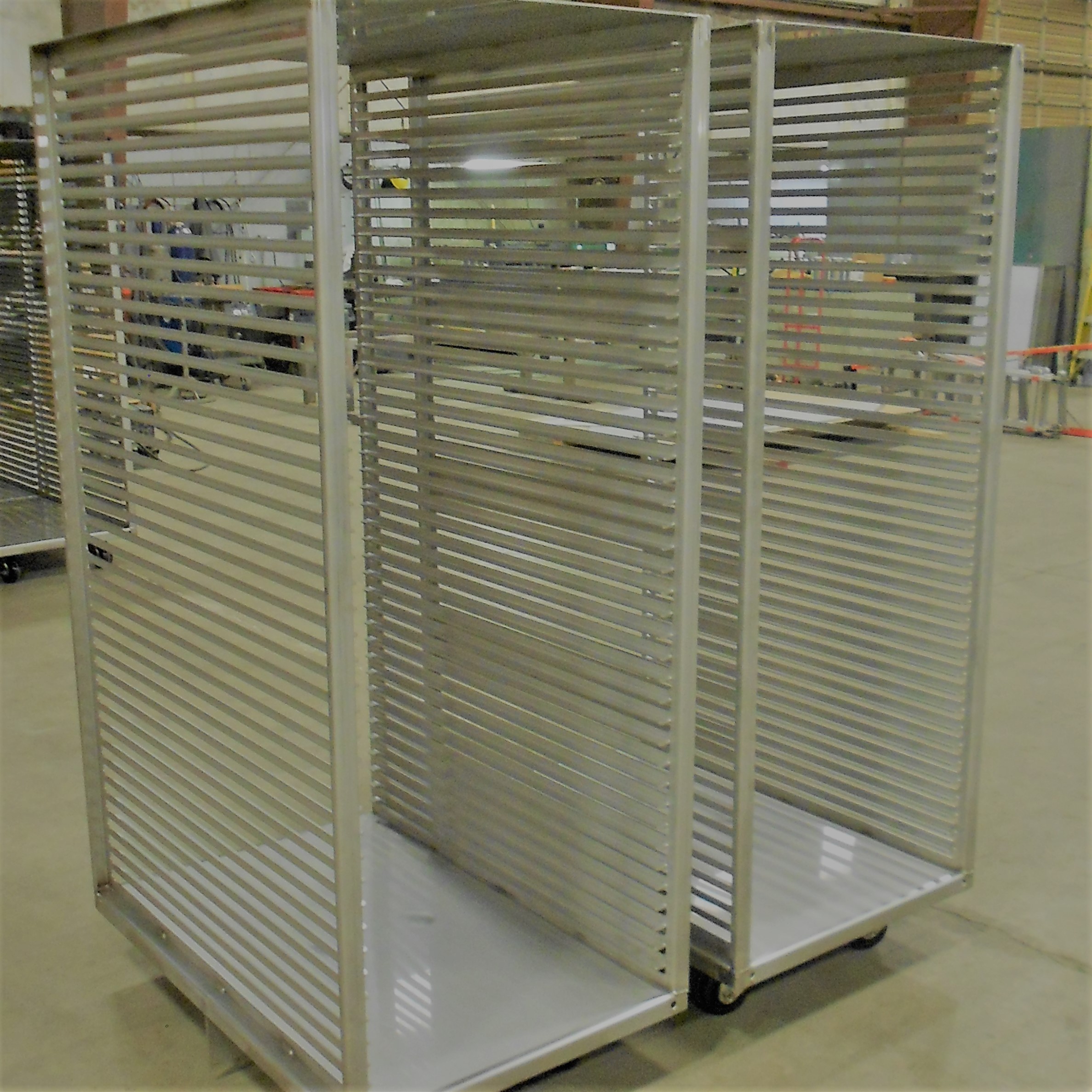
MOBILE TRAY RACKS AND DOLLIES (SOLD SEPARATELY)
Mobile Tray Racks are used with stainless steel trays. Mobile Tray Carts or Dollies are used when self-stacking plastic trays are used. Both are typically made using stainless steel, and are built according to the tray size chosen.
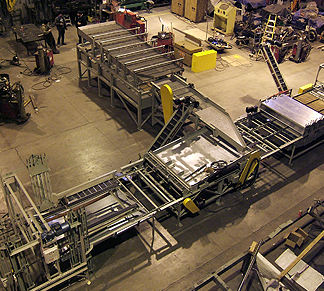
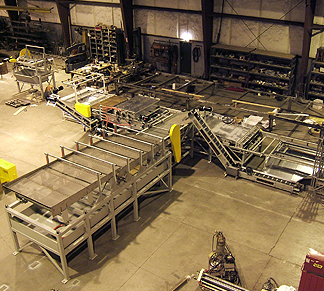
For most products, one traying line can support 12 Tunnel Dryers, when the traying line is operated for one shift per day, and the dryers run 24 hours a day. A second shift doubles the capacity of the traying line, and minimizes the need for extra trays/cars(dollies). A standard traying line includes a elements that are modular in design. The operator has the option to mix and match the elements to the needs of the product that will be run that day.
The trayline is a combination of elements that are combined to meet the unique needs of a single product. The Traying line can be reconfigured at the end of one season into a system that can successfully process additional products. This flexibility accomplished by adding or replacing individual elements within the system, makes the CDS Traying Line highly prized among professional processors.
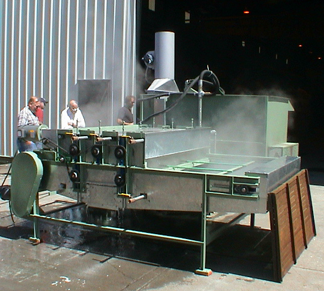
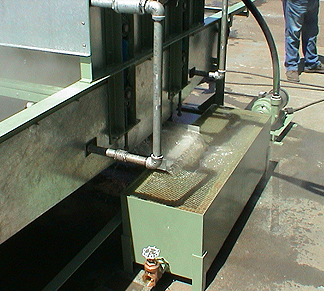
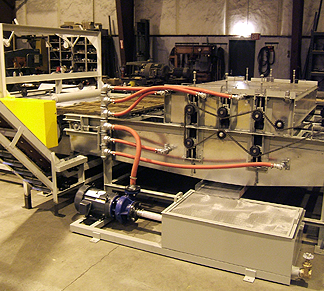
The Tray Washer cleans the tray, and carries the empty tray to the Trayer.
The Tray Washer can be used in line as part of a Traying Line; cleaning trays every time the tray is used, or as a separate system; cleaning the trays only when time allows.
As part of a Traying Line, the Tray Washer receives the tray from the tray scraper, and subjects the tray to water sprays, and rotating brushes. Both top and bottom surfaces are cleaned. As the freshly cleaned tray exits the Tray Washer, the conveyor.
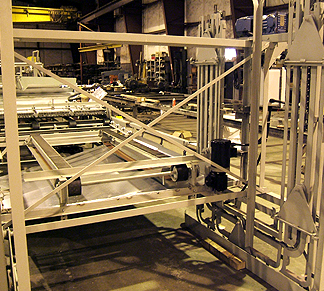
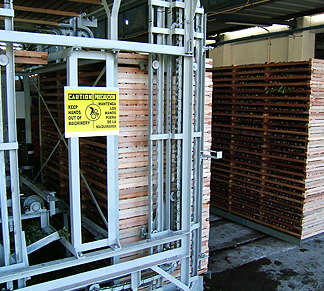
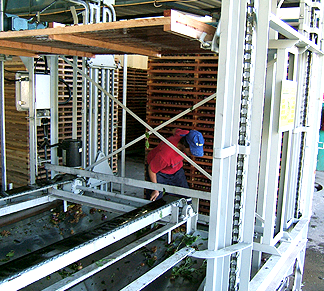
The stacker loads the wet product laden tray on to the Tunnel Car. The Stacker receives the loaded tray from the Trayer/Spreader, and lifts each tray individually, and places the tray on the tray stack supported by the Tunnel Car. The Stacker includes an in-feed conveyor, and Tunnel Car Ram. Like the Trayer/Spreader, the Stacker is available in many sizes, each designed to fit a unique tray size.
The design of the Stacker, model S-72 allows standard wood trays measuring 36 inches, by 72 inches by 3.125 inches thick. Options include stainless steel construction, variable speed controls, and a hydraulic power unit.
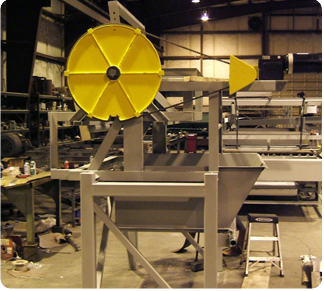
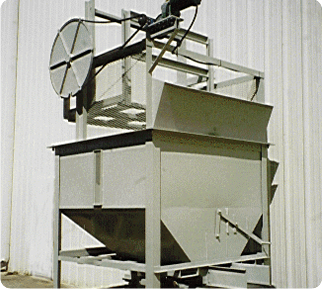
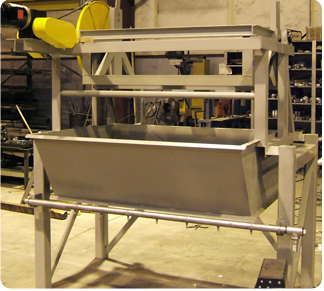
There are several styles of Bin Dumpers available through CDS. They range from simple, robust chain driven systems, mounted above the bulk tank, to multiple (two or four boxes at a time) dumpers supported by in-feed and discharge conveyors with a bin re-stacking function.
The Drawer that Download System, the model BD03, includes an in-food (full) conveyor of drawer, the dumper trucks of drawer (normally a BD02), a carrier of drawer of unloading, and a stacker empty of drawer. Used in applications high volume, the BD03 leads to the maximum effectiveness of a single forklift. The control comes from the board of control of Line of Traying.
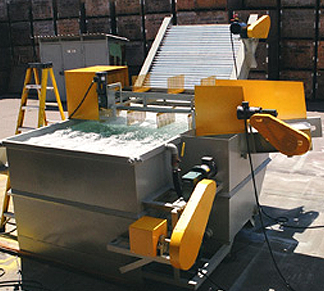
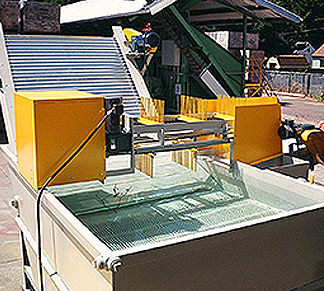
The Bulk Tank provides a cleaning and washing function for fresh fruit and vegetables as they enter the Traying Line. An active "live bottom" agitator gently moves the product towards the discharge elevator. The tank is filled with water, and as the product is poured into the tank, the leaves, trash and other debris are removed from the product stream and carried away on a trash belt. The internal discharge elevator comes with a variable speed control, giving the operators a flexibility not normally available in similar equipment. The Bulk Tank comes in two sizes: 54 inches and 72 inches wide.
Having removed the maximum amount of trash and debris from the product stream, the De-Sticker discharge elevator fills the Clean Green Scale. Included with the scale are the upper hopper with horizontal slide gates, the lower hopper with platform scale, and the discharge elevator. An automated sampling system selects an appropriate amount of clean green product for testing/payment. A digital recorder/printer totals the lot and prints a receipt. Options include stainless steel construction, and variable speed on the elevator, automated slide gates, and upgrades for the scale recorder/printer. Custom configurations (lengths, widths & heights) are available to meet unique needs.
The De-Sticker includes an elevator, and oscillating pan. The elevator lifts the product and a chute spreads the product over the full width of the pan. Perforations in the pan allow the nuts to fall thorough the holes, finger sized sticks continue to the end of the pan and are collected in a trash bin. A hopper below the oscillating pan collects the nuts and feeds an elevator. Options include stainless steel construction, and variable speed drives on the elevators. Custom configurations (lengths, widths & heights) are available to meet unique needs.
The elevator receives the product from the horizontal conveyor, and lifts the product to the Trash Screen. As the product exits the discharge end of the elevator, the air separator forces an air stream up through the product. Rock falls through the air stream and is boxed off. The clean product stream falls into a chute that feeds the Trash Screen. Leaves, husks and nuts with husks attached are blown into the Husker. Options include stainless steel construction.
Each product will have unique elements that will be added the to the basic line. Some products like Apples will use peeling, slicing, coring, while others (like grapes) may only require a fresh water dip. Many of the cut fruit will benefit from exposure to Sulfur Dioxide (SO2) to maintain the very white color of the flesh.
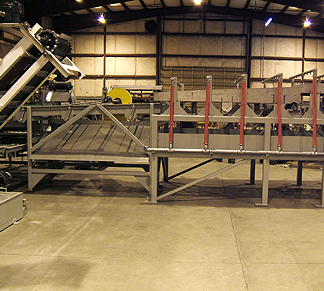
The Leaf Shaker separates leaves, small twigs and other debris from the product stream. Used primarily on whole fruit, the Leaf Shaker also removes most of the surface water from the fruit prior to being loaded on the trays.
The De-Leafer receives the product from the elevator and spreads the nuts across the rough top conveyor. This conveyor mounts at an angle are runs reverse to the flow of the nuts. Small bits of trash, husks, small sticks, and water are removed, while the nuts bounce down toward the air knife. The air knife removes more trash, and husks. Options include stainless steel construction, and variable speed on the conveyor and fan drives. Custom configurations (lengths, widths & heights) are available to meet unique needs.
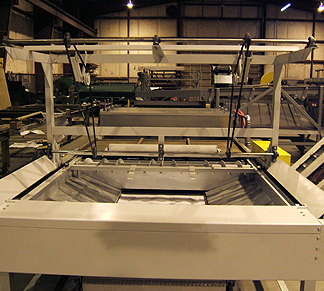
The Scraper removes the dried product from the tray, lifts the product to the boxing belt.
The Scraper removes the dried product from the tray. The product then travels on a conveyor to an elevator; the elevator lifts the dry product into a dry bin or boxing belt (not included with the Scraper). The Scraper utilizes a "soft drop" system that slows the fall of the tray, minimizing damage to the trays and adding useful life/minimizes repairs to the trays. Options include stainless steel construction, variable speed control on the drive chains, and elevator.
The Shaker table functions like the Bulk Tank, but is designed to deal with high volumes of product with lower percentages of trash and debris. A single bin dumper or double bin dumper is used to fill the Shaker Table.
The standard Shaker Table, model ST-01, utilizes multiple spray bars, and oscillating tables to clean and separate the product stream from dust, dirt, and light debris loads. Options include stainless construction, and several sizes to meet increased production needs.
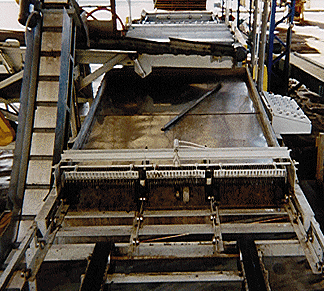
The Spreader applies the wet product on the trays, keeping the product even and consistent.
The task of the Trayer/Spreader is to apply an even product load on the trays conveyed within the system. Often the center piece of a Traying Line, the Trayer includes an oscillating pan, a tray conveyor, spill return system, and clam-shell gate.
The Trayer is available in several sizes, beginning with the 24 inch (width) trays, model TS-24, and extending up to the 72 inch trays, model TS-72. Options include stainless steel construction, variable speed control on the conveyor.
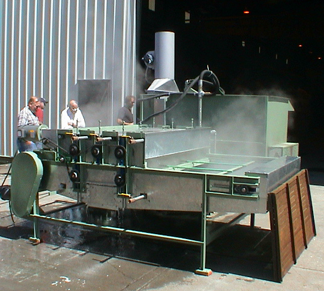
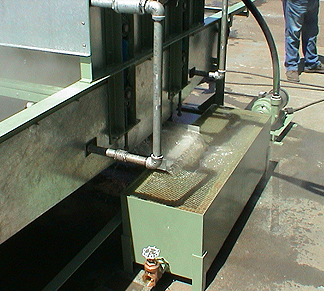
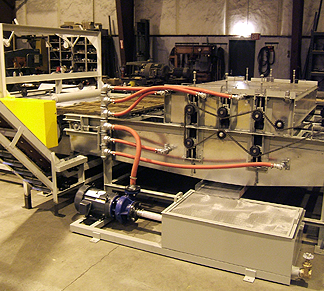
The Tray Washer cleans the tray, and carries the empty tray to the Trayer.
The Tray Washer can be used in line as part of a Traying Line; cleaning trays every time the tray is used, or as a separate system; cleaning the trays only when time allows.
As part of a Traying Line, the Tray Washer receives the tray from the tray scraper, and subjects the tray to water sprays, and rotating brushes. Both top and bottom surfaces are cleaned. As the freshly cleaned tray exits the Tray Washer, the conveyor.